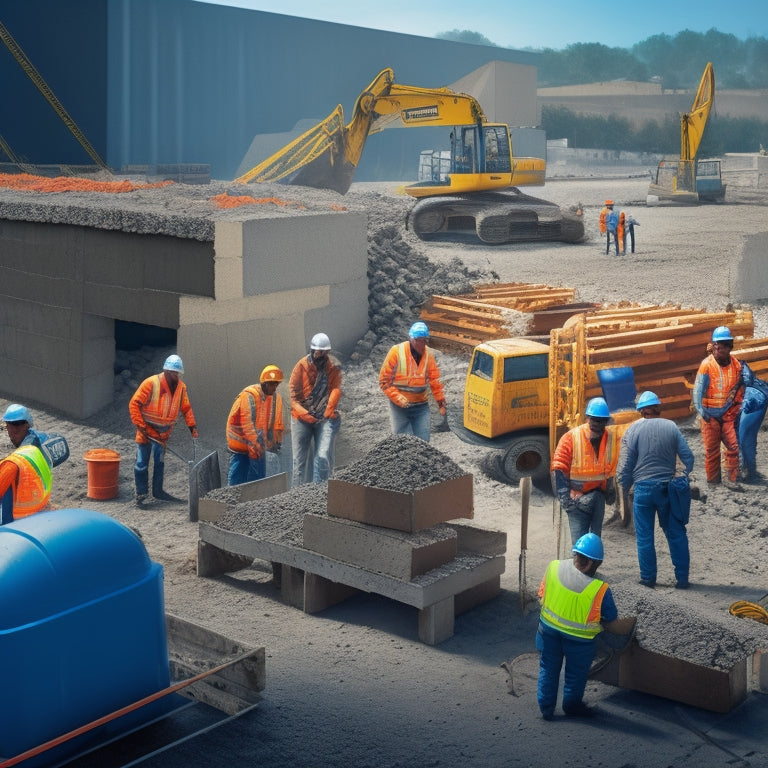
7 Best Tools for Concrete Block Construction
Share
You'll need a solid foundation, precise cutting, and seamless finishing to guarantee your concrete block construction project stands the test of time. Start with essential tools like excavators, grading tools, and leveling instruments to lay a solid foundation. Next, turn to block cutting and shaping tools, such as saws and chisels, to achieve precise fits. Mortar mixing equipment, like mixers and scales, will help you achieve perfect ratios. Then, employ block laying and alignment tools, like string lines and spirit levels, to confirm accurate placement. Leveling and straightening tools, joint filling materials, and finishing techniques will refine your craft. Now, take the next step to excel in these critical tools and techniques.
Key Takeaways
- Excavation tools like backhoes and trenching shovels are essential for digging trenches and preparing the site for concrete block construction.
- Grading tools, including laser levels and plate compactors, ensure accurate grading and soil compaction for a solid foundation.
- Mortar mixing essentials, such as scales and measuring systems, guarantee accurate ingredient measurements for strong mortar.
- Leveling and straightening tools, including laser levels and spirit levels, ensure accurate block placement and alignment.
- Mixing paddles and blades, designed for mortar mixing, contribute to consistent mixes and prevent lumps for a smooth texture.
Laying the Foundation Tools
When building a concrete block structure, a solid foundation is essential to guarantee stability and prevent settling or cracking. You'll need to design a precise foundation layout, considering the soil type, water table, and environmental factors.
To achieve this, you'll require specialized tools for excavation and site preparation. For excavation, you'll need a backhoe or excavator to dig the foundation trenches and a trenching shovel for manual excavation.
A laser level guarantees accurate grading and leveling of the site. A plate compactor or hand tamper helps compact the soil, preventing settling and guaranteeing a stable base.
To create a level foundation, you'll need a transit level or rotating laser level to establish a reference point. A string line and stakes will help you mark the foundation layout, while a chalk line and straightedge guarantee straight lines and accurate corners.
With these tools, you'll be able to create a solid foundation that supports your concrete block structure.
Block Cutting and Shaping
When you're working with concrete blocks, you'll need to make precise cuts to fit them together seamlessly.
You'll also need to shape blocks to fit around corners, curves, and other obstacles.
To achieve professional-looking results, you'll want to perfect precise cutting techniques, learn effective block shaping methods, and investigate edge profiling options.
Precise Cutting Techniques
You'll need to master precise cutting techniques to achieve professional-looking results in concrete block construction. An essential aspect of this is cutting safety, which involves wearing protective gear, ensuring a stable work environment, and maintaining a firm grip on your tools. Tool maintenance is also important, as dull blades can lead to inaccurate cuts and increased risk of accidents.
To achieve precise cuts, consider the following techniques:
Technique | Description |
---|---|
Score and Break | Score the block lightly with a hammer and chisel, then break it along the score line |
Saw Cutting | Use a masonry saw or a circular saw with a masonry blade to make clean, straight cuts |
Nibbling | Use a carbide-tipped nibbler to remove small pieces of concrete, ideal for curved cuts |
Chiseling | Use a chisel and hammer to remove small amounts of concrete, suitable for irregular shapes |
Grinding | Use a grinder to smooth out rough edges and remove excess concrete |
Block Shaping Methods
Becoming proficient in precise cutting techniques is just the starting point in concrete block construction.
You'll also need to shape the blocks to fit your specific design requirements. This is where block shaping methods come in. You can use various block types, each suited for specific applications. For instance, you'll use split-face blocks for exposed aggregate finishes, while smooth-faced blocks are ideal for painted or stuccoed surfaces.
To achieve the desired shape, you'll need shaping molds. These molds come in different shapes and sizes, allowing you to create unique block profiles.
You can use manual or hydraulic presses to force the concrete into the mold, depending on the scale of your project. When choosing a shaping mold, consider the block type, desired finish, and the pressure required to achieve the desired shape.
Edge Profiling Options
During the concrete block construction process, achieving precise edge profiles is essential for a strong and durable structure. You'll need to choose the right tools to guarantee accurate edge profiling, which involves cutting and shaping blocks to fit together seamlessly.
For edge profiling, you'll require a combination of power saws and handheld tools. A diamond blade saw is ideal for cutting blocks to size, while a grinder or a rotary hammer is better suited for edge finishing. These tools enable you to achieve precise angles and profiles, assuring a snug fit between blocks.
When it comes to corner detailing, using a combination of masonry chisels and carbide-tipped hand saws allows for precise trimming and fitting of blocks. Additionally, a corner profiler or a corner cutter can be used to create precise 90-degree angles, assuring a strong and stable structure.
Mortar Mixing Essentials
When you're working with concrete blocks, you need a strong, consistent mortar to hold them together.
To achieve this, you'll need to get your mixing ratios right, choose the right mixer machine for the job, and simplify the batching process.
Mixing Ratios Explained
You're about to lay the foundation of a sturdy structure, and that foundation begins with the right mixing ratio. A good mixing ratio is vital for achieving the desired strength, workability, and durability of your concrete blocks.
When it comes to mixing ratios, you need to get it right to avoid costly mistakes and guarantee your structure stands the test of time.
Here are the essential factors to take into account for accurate ratio calculations:
-
Cement-to-sand ratio: The ideal ratio ranges from 1:2 to 1:4, depending on the type of cement and the desired strength.
-
Water-to-cement ratio: The recommended ratio is typically between 0.4 and 0.6, but this can vary depending on the ambient temperature and humidity.
-
Aggregate-to-cement ratio: The ratio of aggregate (sand, gravel, or crushed stone) to cement affects the workability and strength of the mix.
- Additives and admixtures: Take into account the type and amount of additives, such as fly ash or silica fume, and admixtures, like air-entraining agents or retarding agents, that can impact the mixing ratio.
Mastering mixing techniques and ratio calculations will help you achieve a consistent, high-quality mix that meets your project's specific requirements.
Mixer Machine Options
With your concrete block construction project underway, turning to the right mixer machine is essential for efficient and effective mortar mixing. You'll want to take into account factors like power source, capacity, and portability when selecting the ideal mixer for your needs.
Mixer Type | Power Source | Capacity |
---|---|---|
Portable Mixer | Electric or Gas | 1-3 cu. ft. |
Electric Mixer | Electric | 3-6 cu. ft. |
Heavy-Duty Mixer | Electric or Gas | 6-12 cu. ft. |
Concrete Mixer | Electric or Gas | 12-24 cu. ft. |
Tow-Behind Mixer | Gas | 24-40 cu. ft. |
Portable mixers are ideal for small to medium-sized projects, offering ease of transport and versatility. Electric mixers provide a reliable and consistent power source, while heavy-duty mixers are suited for large-scale projects requiring high-volume mixing. When choosing a mixer, reflect on the size and scope of your project, as well as the power source and capacity you require. By selecting the right mixer machine, you'll be well on your way to efficient and effective mortar mixing.
Batching Made Easy
Batching Made Easy (Mortar Mixing Essentials)
Having selected the right mixer machine for your concrete block construction project, you can now focus on the mortar mixing process itself. Accurate batching is vital to guarantee the quality and consistency of your concrete blocks. To achieve this, you'll need to measure and mix the right proportions of cement, sand, and water.
Here are the essential mortar mixing components to evaluate:
-
Batching automation: Invest in an automated batching system to streamline the process and minimize errors. This technology allows for precise measurement and mixing of ingredients, saving you time and resources.
-
Mobile batching: Think about a mobile batching system for on-site mixing, especially for large projects or those with limited storage space. This flexibility enables you to batch and mix materials wherever needed.
-
Scales and measuring systems: Guarantee accurate measurement of ingredients with high-quality scales and measuring systems. These tools help you achieve the perfect mix ratio and avoid costly mistakes.
- Mixing paddles and blades: Use durable, high-performance mixing paddles and blades specifically designed for mortar mixing. These components help you achieve a consistent, lump-free mix.
Block Laying and Alignment
During the early stages of concrete block construction, proper block laying and alignment are essential to guarantee a strong and durable structure.
You'll need to create a block layout that guarantees accurate spacing and alignment of the blocks. This can be achieved by using a string line and a level to mark the block positions on the footing or wall base.
Alignment techniques, such as the "bump and check" method, can help you maintain a straight line and correct any deviations. To ascertain accurate block placement, use a spirit level to check the block's position and a torpedo level to check the wall's plumbness.
Additionally, use a line and pin system to maintain a consistent block layout and alignment. By following these techniques, you can guarantee that your concrete block structure is built on a solid foundation, with accurately aligned blocks that provide maximum strength and stability.
Leveling and Straightening
Your concrete block structure's foundation is only as strong as its leveling and straightening. Proper leveling guarantees the blocks are laid on a perfectly horizontal surface, while straightening assures the walls are plumb and even.
To achieve this, you'll need the right tools.
Here are the essential tools for leveling and straightening your concrete block structure:
-
Laser Leveling Tool: This tool projects a level line or plane onto the surface, allowing you to accurately check and adjust the block's position.
-
Spirit Level: A precision spirit level helps you verify the block's orientation and make precise adjustments.
-
Straightening Tools: These include long, straight edges and strings with levels attached, which help you check and correct the wall's straightness.
- Tamping Tool: A tamping tool helps settle the sand or gravel base, guaranteeing a stable foundation for your blocks.
Joint Filling and Finishing
Fill in the gaps between your concrete blocks with precision and care, as the joints hold the key to a strong and durable structure. The joint filling process involves selecting the right joint materials for your project, such as mortar, grout, or sealants. Choose materials that match the color and texture of your concrete blocks to guarantee a seamless finish.
When filling joints, use a pointing trowel or jointer to spread the material evenly and remove excess. For larger joints, consider using a grout pump or mixer to speed up the process.
Once the joints are filled, it's time to finish them. Finishing techniques, such as tooling or striking, help to compact the joint material and remove excess. You can also use a joint finishing tool to create a concave or V-shaped joint.
Proper finishing techniques guarantee a strong bond between the joint material and the concrete blocks, preventing water infiltration and structural damage. By following these steps, you'll achieve professional-looking joints that add to the overall integrity of your concrete block structure.
Final Inspection and Touch-ups
Inspecting your concrete block structure from top to bottom, you're scrutinizing every detail to ascertain a job well done.
This final inspection is vital for verifying the structure meets the required safety protocols and quality assurance standards.
You're checking for any defects, damage, or irregularities that may have occurred during construction. This includes verifying that all joints are properly filled and finished, and that the structure is level, plumb, and square.
Here is your final checklist:
- Verify structural integrity: Ascertain the structure can withstand the intended loads and stresses.
- Check for defects: Inspect for any cracks, damage, or irregularities in the concrete blocks or mortar.
- Confirm quality of finish: Verify that the finish meets the required standards, including texture, color, and smoothness.
- Confirm compliance with regulations: Verify that the structure meets all relevant building codes, regulations, and safety standards.
Frequently Asked Questions
Can I Use Concrete Blocks for Load-Bearing Walls and Structures?
You can definitely use concrete blocks for load-bearing walls and structures, leveraging their advantages, such as high compressive strength and durability, to guarantee a strong load-bearing capacity that meets your building's requirements.
How Do I Ensure Proper Drainage in Concrete Block Construction?
Did you know that 75% of structural damage is caused by water intrusion? You'll want to guarantee proper drainage in concrete block construction by designing effective drainage systems and implementing moisture management strategies to prevent water accumulation and damage.
What Safety Precautions Should I Take When Working With Concrete Blocks?
When working with concrete blocks, you should take safety precautions, such as wearing dust protection gear and using proper block lifting techniques to avoid injuries and respiratory issues.
Can I Use Recycled Concrete Blocks for New Construction Projects?
You can consider using recycled concrete blocks for new construction projects, as they offer sustainability benefits and can be a cost-effective option after conducting a thorough cost effectiveness analysis, ensuring they meet project requirements.
How Do I Protect Concrete Blocks From Weather Damage and Erosion?
Imagine concrete blocks exposed to harsh weather, pores absorbing water like a sponge. You'll prevent erosion by applying moisture barriers and choosing the right sealant options, such as silane or siloxane-based products, to protect your blocks from water infiltration and damage.
Conclusion
As you stand back to admire your concrete block construction, the fruits of your labor come into sharp focus. Like a skilled puzzle, every block clicks into place, a proof of your precision and skill. With the right tools by your side, the process unfolds like an orchestra, each step harmonizing with the next. The end result? A sturdy, imposing structure that exudes strength and durability, a true masterpiece born from the marriage of art and engineering.
Related Posts
-
Essential Tools for Concrete Wall Covering Projects
When tackling a concrete wall covering project, you'll need a range of essential tools and equipment. For cleaning an...
-
Budget-Friendly Tools for DIY Decorative Concrete Profiling
You can achieve professional-grade decorative concrete results on a budget by investing in the right combination of e...
-
Top Tools for Concrete Adhesion Success
When it comes to concrete adhesion success, you'll need to wield the right tools and techniques to guarantee a strong...