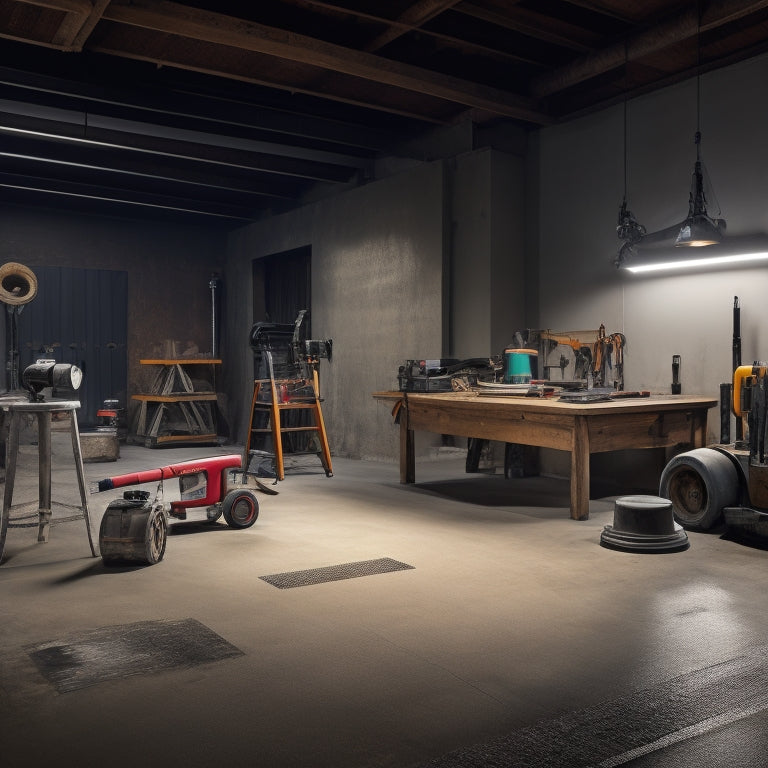
7 Must-Have Tools for a Polished Concrete Finish
Share
When tackling a polished concrete project, you'll need the right tools to achieve a high-gloss finish that meets industry standards. Start with grinders and polishers for smooth finishing and high-gloss results. Diamond pads with a structured grit sequence are essential for effective scratch removal and surface refinement. Edgers make certain clean corners, while densifiers and sealers provide hardened surfaces and long-lasting protection. Measurement and leveling tools, such as concrete depth gauges and laser leveling tools, assure accurate application and a perfectly level surface. With these seven must-have tools, you'll be well on your way to a flawless finish - and understanding the nuances of each tool will take your project to the next level.
Key Takeaways
• Grinders and polishers are essential for removing imperfections and achieving a smooth concrete surface with a high-gloss finish.
• Diamond pads and a structured grit sequence are critical for achieving a polished surface, with metal-bonded pads for coarse grinding and resin-bonded for fine polishing.
• Edgers and corner finishing tools are necessary for clean corners and seamless transitions between corners and main areas.
• Densifiers and sealers are required to harden surfaces, provide stain and abrasion protection, and offer long-lasting protection against damage.
• Measurement and leveling tools, such as concrete depth gauges and laser leveling tools, ensure accurate measurements and a perfectly level surface for polished concrete.
Grinders for Smooth Finishing
When preparing a concrete surface for a polished finish, you'll need a reliable grinder to remove imperfections and achieve a smooth, even base. A grinder is an essential tool in concrete surface preparation, allowing you to eliminate cracks, unevenness, and other defects that can compromise the final result.
However, it's vital to follow strict grinder safety practices to avoid accidents and guarantee a successful outcome. Always wear protective gear, including gloves, safety glasses, and a dust mask, and make certain the grinder is properly maintained and in good working condition.
Choose a grinder that suits your specific needs, considering factors such as power, speed, and versatility. A high-torque grinder with variable speed control is ideal for most concrete surface preparation tasks.
Additionally, consider the type of grinding wheel or disc you'll need, as different materials and grit levels are suited to specific applications. By selecting the right grinder and following proper safety protocols, you'll be well on your way to achieving a flawless, polished concrete finish that meets your high standards.
Concrete Polishing Diamond Pads
When you're working with concrete polishing diamond pads, you'll quickly realize that the right pad selection is essential to achieving a high-gloss finish.
You'll need to understand the importance of following a specific grit sequence to progressively refine the concrete surface.
Pad Selection Matters
How do you guarantee a flawless polished concrete finish without the right diamond pads, bearing in mind they're the primary interface between your equipment and the concrete surface? The answer lies in pad selection. With so many options available, it's essential to choose the right pad for your project.
Here are some key factors to take into account:
-
Pad types: Metal-bonded pads are ideal for coarse grinding, while resin-bonded pads are better suited for fine polishing. Hybrid pads offer a balance between the two.
-
Pad sizes: Larger pads (16-20 inches) cover more surface area, but may be difficult to maneuver in tight spaces. Smaller pads (12-14 inches) provide more control, but slow down the process.
-
Bond strength: Softer bonds are used for softer concrete, while harder bonds are used for harder concrete.
Grit Sequence Importance
Your polished concrete finish hinges on a well-planned grit sequence, as it dictates the effectiveness of your diamond pads in removing scratches and achieving a high-gloss finish. A well-structured grit sequence guarantees that each pad builds upon the previous one, progressively refining the surface. This sequence also helps you optimize the benefits of each grit type, from aggressive metal-bonded pads to fine resin-bonded pads.
Grit Type | Grit Benefits |
---|---|
Metal-Bonded (16, 30) | Aggressive scratch removal, high stock removal rate |
Hybrid-Bonded (50, 100) | Balanced scratch removal and surface refinement |
Resin-Bonded (200, 400) | Fine scratch removal, high-gloss finish |
Ceramic-Bonded (800, 1500) | Ultra-fine scratch removal, high-reflectivity finish |
Polishing Pads (3000, 6000) | Final polish, high-gloss finish |
Proper Pad Maintenance
Effective pad maintenance is essential to extending the life of your concrete polishing diamond pads, ensuring they continue to deliver optimal performance and results throughout the polishing process.
You've invested in high-quality pads, and with proper care, they'll continue to provide ideal results. To get the most out of your pads, it's vital to develop a routine maintenance plan.
Here are some key considerations to keep in mind:
-
Clean your pads regularly: Develop a pad cleaning technique that works for you, such as using a pressure washer or a gentle scrub brush to remove debris and residue. This will prevent the buildup of materials that can compromise your pad's performance.
-
Store your pads properly: Invest in pad storage solutions that keep your pads organized, protected, and dry. This will prevent damage, corrosion, and premature wear.
-
Monitor pad wear and tear: Regularly inspect your pads for signs of wear, such as uneven edges or excessive diamond loss. This will help you identify when it's time to replace your pads, ensuring you always have the best tools for the job.
Edgers for Clean Corners
You'll need an edger that can navigate tight spaces and maintain a consistent angle to achieve clean, precise corners in your polished concrete finish.
When it comes to edger types, you'll have to decide between walk-behind edgers, ride-on edgers, and handheld edgers. Each type has its strengths and weaknesses, but for corners, handheld edgers are often the best choice. They offer greater control and precision, allowing you to get into tight spaces and maintain a consistent angle.
When it comes to corner techniques, there are a few strategies to keep in mind. The 'push-pull' method involves pushing the edger into the corner and then pulling it back out, repeating the process until the desired level of polish is achieved.
The 'overlap' method involves overlapping passes to guarantee a seamless shift between the corner and the main floor area. Regardless of the technique you choose, it's crucial to maintain a consistent angle and pace to avoid leaving swirl marks or other imperfections.
Densifiers for Hardened Surfaces
Densification is a vital step in the polished concrete process, as it transforms the porous, absorbent surface into a hardened, impermeable one. That's where densifiers come in. You'll need to apply a chemical densifier to the concrete surface to fill in the pores and create a dense, solid foundation for your polished finish.
When it comes to choosing a densifier, you've got options. Here are a few things to take into account:
-
Silicate-based densifiers: These are the most common type and work well for most polished concrete applications.
-
Silane-based densifiers: These are more expensive, but offer superior protection against stains and abrasion.
-
Lithium-based densifiers: These are a newer option that offers improved durability and stain resistance.
Regardless of which type you choose, proper application techniques are essential. Make sure to follow the manufacturer's instructions and apply the densifier in thin, even coats to avoid over-saturating the concrete.
Sealers for Long-Lasting Protection
With your newly densified surface in place, now it's time to apply a sealer to protect your polished concrete from stains, spills, and everyday wear and tear.
You have two primary options: water-based sealers and solvent-based sealers. Water-based sealers are eco-friendly, non-toxic, and offer excellent UV protection. Solvent-based sealers, on the other hand, provide a higher gloss finish but have stronger fumes and higher VOCs.
Regardless of your choice, proper surface preparation is essential. Make sure your concrete is clean, dry, and free of imperfections before application.
Next, consider the application technique, as this can affect the sealer's performance. Most sealers require a thin, even coat, with drying times ranging from 30 minutes to several hours.
When comparing costs, factor in the sealer's durability, maintenance schedules, and user reviews.
Polishers for High-Gloss Finish
Polishers for High-Gloss Finish
Achieving a high-gloss finish requires precision polishing, which is where high-performance polishers come into play, offering superior cutting power and refined finish control.
You'll need to choose the right polisher type and polishing technique to attain the desired level of shine.
When it comes to polisher types, you have options:
-
Rotary polishers: Ideal for rapid material removal and aggressive cutting, these polishers are perfect for the initial stages of polishing.
-
Orbital polishers: Suitable for finer polishing and finishing, these machines provide a high-gloss finish without leaving scratches or swirl marks.
-
Edge polishers: Designed for polishing edges, curves, and tight spaces, these specialized tools guarantee a flawless finish in hard-to-reach areas.
Measuring Tools for Accurate Application
When you're working on a polished concrete finish, you can't afford to guess or estimate - you need precise measurements to guarantee a flawless result.
That's where measuring tools come in, and you'll want to have a few essentials on hand.
You'll be using tools like concrete depth gauges and laser leveling tools to get accurate readings and achieve a perfect finish.
Concrete Depth Gauges
You'll need a concrete depth gauge to accurately measure the thickness of your concrete slab, guaranteeing a uniform and polished finish. A precise concrete thickness measurement is vital to achieve the desired outcome. A depth gauge guarantees that your concrete is poured to the correct depth, which affects the overall strength and durability of the slab.
Here are some essential features to look for in a concrete depth gauge:
-
High-precision measurement: Look for gauges that provide accurate readings to the nearest 1/16 inch or 1 mm.
-
Durable construction: A rugged design guarantees the gauge withstands the demands of a construction site.
-
Easy-to-read display: A clear and intuitive display makes it simple to take readings and track progress.
With a reliable concrete depth gauge, you'll be confident that your concrete slab meets the required specifications. This accuracy translates to a polished finish that's both aesthetically pleasing and structurally sound.
Laser Leveling Tools
Accurate leveling is essential to achieving a polished concrete finish, and laser leveling tools provide the precision needed to confirm your concrete slab is perfectly horizontal and vertically aligned. You can't rely on traditional leveling techniques alone, as they often fall short of the required accuracy.
Laser leveling tools, on the other hand, utilize advanced technology to ascertain laser accuracy, providing a precise reference point for your entire project.
When it comes to leveling techniques, you'll need a tool that can accurately measure and adjust the concrete slab's elevation. Laser leveling tools accomplish this by projecting a level line or plane onto the surface, allowing you to identify and correct any deviations. This results in a perfectly level surface, which is critical for a polished concrete finish.
Frequently Asked Questions
Can I Achieve a Polished Concrete Finish on an Old or Damaged Floor?
You can revive an old or damaged floor with a polished concrete finish, but first, you'll need to employ advanced repair techniques and thorough surface preparation to guarantee a strong, even base for a flawless finish.
How Long Does the Entire Polishing Process Typically Take to Complete?
As you commence on this odyssey of floor refinement, you'll find the polishing timeline is a function of process factors, like floor size, condition, and desired gloss level, typically taking anywhere from a few days to several weeks to complete.
Is It Necessary to Use a Densifier on a Newly Poured Concrete Floor?
When you're working with a newly poured concrete floor, you'll want to apply a densifier to enhance durability and stain resistance; proper application techniques guarantee ideal densifier benefits, including improved abrasion resistance and reduced maintenance.
Can I Use a Grinder for Both Concrete Grinding and Polishing?
You can use a concrete grinder for both grinding and polishing, but it depends on the type of grinder and your grinding techniques; for example, a planetary grinder is ideal for polishing, while a rotary grinder is better suited for aggressive grinding.
Are Polished Concrete Floors Suitable for High-Traffic Commercial Areas?
You'll be surprised to know that 80% of commercial buildings use polished concrete floors, and yes, they're suitable for high-traffic areas, but you'll need to take into account durability concerns and maintenance requirements to guarantee their longevity.
Conclusion
You've now got the essential tools for achieving a polished concrete finish that's both durable and visually stunning.
Curiously, the polished concrete market is expected to reach $3.4 billion by 2025, with the commercial sector driving demand.
With these 7 must-have tools, you'll be well-equipped to capitalize on this growing trend and deliver high-quality results that exceed client expectations.
Related Posts
-
Concrete Foundation Building Tools for Homeowners' Success
As you start your concrete foundation building project, it is vital to have the right tools to guarantee success. You...
-
Free Design Tools for Concrete House Planning
You can kick-start your concrete house planning project without breaking the bank, as there are several free design t...
-
5 Tips for Splitting Concrete With Second-Hand Tools
When splitting concrete with second-hand tools, you'll need to be strategic to avoid wasting time, money, and putting...