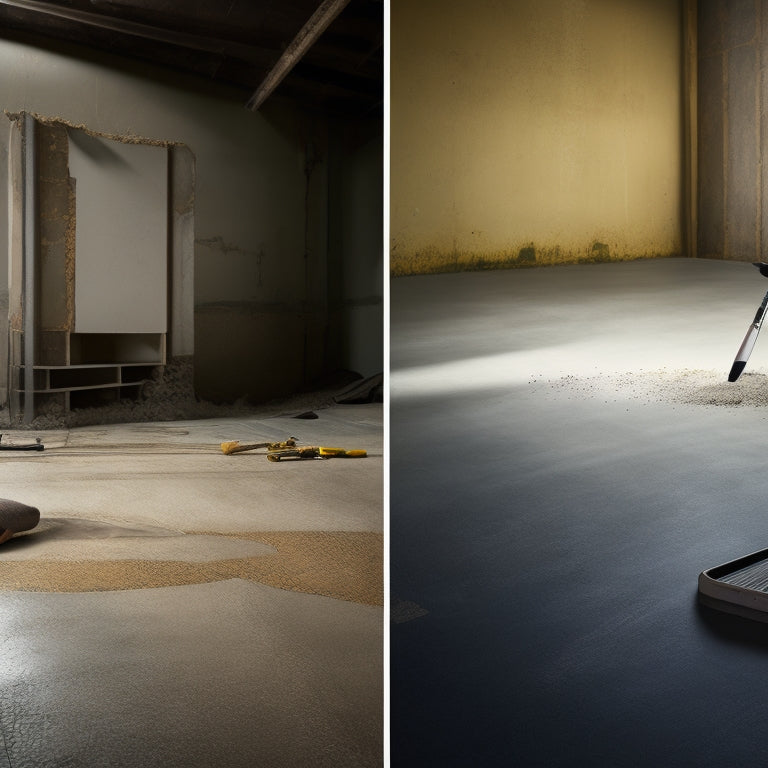
7 Best Tools for Concrete Sealing Compared
Share
You're about to tackle a concrete sealing project, and the right tools are essential for a professional-looking finish. For silane-based sealers, high-quality sprayers or rollers guarantee even distribution. Acrylic sealers require HVLP sprayers with adjustable pressure and flow rates. Epoxy coatings demand precise roller material selection, while polyurethane sealers benefit from natural or synthetic brushes. Applicator guns, pump systems, and laminator tools also play vital roles. With so many options, choosing the best tool for your project can be intimidating. As you explore your options, you'll want to take into account the specific requirements of your sealer and the job at hand.
Key Takeaways
• High-quality sprayers or rollers are essential for even distribution and uniform, thin coats for proper penetration into concrete.
• The right brush or roller material choice is critical for specific sealer types, such as epoxy coatings, to ensure effective sealing and easy cleanup.
• Applicator guns for sealants require careful nozzle selection to achieve uniform application, and features like detachable nozzles simplify cleaning.
• Pump systems for water-based sealers need to maintain at least 100 psi pressure and have durable, kink-resistant hoses for efficient application.
• Low-VOC sealer laminator tools provide precise control over application techniques, achieving consistent, thin layers of sealer for peak performance.
Silane-Based Sealer Application Tools
When applying silane-based sealers, you'll need a range of specialized tools to guarantee a successful, long-lasting seal. Silane properties, such as their ability to penetrate deep into the concrete, require specific application tools to maximize their effectiveness.
First and foremost, you'll need a high-quality sprayer or roller to evenly distribute the sealer onto the surface. The sprayer or roller should be capable of applying a uniform, thin coat to make certain the silane sealer can penetrate the concrete properly. Additionally, you'll need a variety of brushes and rollers in different sizes to reach tight spaces and corners.
Surface preparation is also essential when applying silane-based sealers. You'll need a wire brush or scrubber to remove dirt, oil, and other contaminants from the surface. A degreaser may also be necessary to clean the surface before application.
Moreover, you may need a wet/dry vacuum to remove any standing water or debris from the surface. By having the right tools for the job, you can make certain a successful, long-lasting seal that protects your concrete from damage.
Acrylic Sealer Spraying Equipment
You'll require a different set of spraying equipment for acrylic sealers, which are formulated to provide a protective film on the concrete surface, rather than penetrating it like silane-based sealers. Acrylic sealers offer benefits such as ease of application, high gloss finish, and UV resistance. To capitalize on these benefits, you'll need the right equipment.
When it comes to application techniques, you'll want to use a sprayer that can handle the thicker, more viscous consistency of acrylic sealers. A high-volume, low-pressure (HVLP) sprayer is an excellent choice, as it provides a uniform, fine spray pattern that minimizes over-spray and guarantees a smooth, even finish.
Look for a sprayer with adjustable pressure and flow rates to customize the application to your specific needs. Additionally, consider a sprayer with a reversible tip to make cleaning easier and reduce clogs.
Epoxy Coating Roller Systems
When you're working with epoxy coating roller systems, you'll want to take into account a few key factors to guarantee a successful application.
You'll need to think about how to achieve even coating distribution, which roller material options will work best for your project, and how to make cleanup a breeze.
Even Coating Distribution
Achieving an even coating distribution is essential for effective concrete sealing, and epoxy coating roller systems are designed to guarantee uniform application by allowing for precise control over the amount of coating dispensed onto the substrate. As you prepare to seal your concrete surface, you'll want to focus on even coating techniques to verify a professional-looking finish.
Coating Thickness | Surface Preparation | Desired Finish |
---|---|---|
Thin (10-20 mils) | Light sanding, cleaning | High-gloss, smooth |
Medium (20-40 mils) | Medium sanding, etching | Satin, semi-gloss |
Thick (40-60 mils) | Aggressive sanding, profiling | Matte, textured |
Roller Material Options
Three primary roller material options are available for epoxy coating roller systems: foam, microfiber, and lambswool, each with its unique characteristics and benefits that can greatly impact the sealing process.
You'll want to contemplate the roller material durability and how it affects the overall performance of your epoxy coating application. Foam rollers, for instance, are lightweight and easy to maneuver, but may lack the durability of other options. Microfiber rollers, on the other hand, offer exceptional roller material durability and are ideal for applying thin, even coats. Lambswool rollers, with their natural fiber texture, provide an excellent balance between durability and texture retention.
When choosing a roller material, you should also reflect on the roller material textures and how they interact with your concrete surface. For example, microfiber rollers are best suited for smooth surfaces, while lambswool rollers are more effective on textured or rough surfaces.
Ease of Cleanup
You'll find that the ease of cleanup with epoxy coating roller systems is directly tied to the roller material you've chosen, as some materials will leave behind residual adhesive or fibers that can be difficult to remove.
For instance, rollers with foam or microfiber covers tend to be more challenging to clean than those with nylon or polyester covers.
When it comes to cleanup techniques, it's important to act quickly to prevent the epoxy coating from drying and setting on the roller.
Use a gentle cleaning product specifically designed for removing epoxy, and avoid using harsh chemicals or abrasive materials that can damage the roller.
It's also vital to choose the right cleanup products for the job, such as solvents or cleaning solutions that are compatible with the epoxy coating and roller material.
Polyurethane Sealer Brush Options
When applying polyurethane sealer, selecting the right brush is essential, as it directly affects the even distribution and finish of the sealant. You'll want to choose a brush that guarantees a smooth, even coat, which is critical to achieving the best possible polyurethane durability.
For sealer application techniques, natural bristle brushes are often preferred, as they hold a lot of material and apply it evenly. However, they can leave brush strokes, which may be visible on the finished surface. On the other hand, synthetic brushes, like nylon or polyester, produce a smoother finish but may not hold as much material.
Another factor to take into account is the brush's nap length. A longer nap length is better suited for applying thicker coats, while a shorter nap length is ideal for thinner coats.
You may also want to reflect on the brush's handle material, as it affects the overall durability and comfort of the brush. By selecting the right brush, you can guarantee a professional-looking finish and achieve the best possible results from your polyurethane sealer.
Concrete Sealer Applicator Guns
When selecting a concrete sealer applicator gun, you'll want to take into account the type and options that best suit your project's needs.
You'll also need to reflect on the nozzle size and material, as these factors can affect the quality of the sealant application.
Gun Types and Options
Three primary types of concrete sealer applicator guns are available on the market: siphon guns, piston guns, and spray guns, each designed to cater to specific sealing needs and preferences. When choosing the right gun type, you'll want to evaluate factors such as the size of your project, the type of sealer you're using, and your personal comfort level with the applicator.
Here's a breakdown of each gun type and their key characteristics:
Gun Type | Description |
---|---|
Siphon Gun | Uses suction to draw sealer from a container, ideal for small to medium-sized projects |
Piston Gun | Uses a piston to push sealer through the hose, suitable for medium to large-sized projects |
Spray Gun | Uses compressed air to spray sealer, best for large-scale projects or those requiring a high level of precision |
When selecting an applicator, you'll also want to evaluate additional options such as hose length, material, and tip size. By understanding the different gun types and options available, you'll be able to choose the best tool for your specific concrete sealing needs.
Nozzle Size and Material
With the gun type selected, you'll need to evaluate the nozzle size and material, as these factors greatly influence the precision and efficiency of your concrete sealing application.
The nozzle size determines the width of the sealer stream, which affects the coverage rate and uniformity of application. A smaller nozzle is ideal for intricate areas, while a larger one is better suited for large, open spaces.
Nozzle material is also essential, as it affects durability and resistance to corrosion. Stainless steel and polyurethane nozzles are popular choices due to their resistance to wear and tear.
Additionally, consider the nozzle shape, as it impacts the sealer's flow pattern. Cone-shaped nozzles provide a focused stream, while fan-shaped nozzles disperse the sealer more widely.
When selecting a nozzle, confirm it's compatible with your chosen gun type and sealer. Nozzle compatibility is critical to prevent clogging, leaks, and poor performance.
Look for nozzles with a secure attachment mechanism, such as threads or clips, to guarantee a tight seal.
Ease of Cleaning
You'll find that a concrete sealer applicator gun's ease of cleaning greatly impacts the overall efficiency of your sealing project, as a clogged or dirty gun can lead to wasted time, material, and labor. A gun that's easy to clean will save you time and effort in the long run, allowing you to focus on completing your project quickly and effectively.
When evaluating a concrete sealer applicator gun's ease of cleaning, look for features such as detachable nozzles, easy-to-access chambers, and smooth, non-stick surfaces. These design elements will make it simpler to remove dried sealer and debris, reducing the risk of clogs and blockages. Additionally, consider the type of cleaning solutions you'll need to use, as some guns may require specialized cleaners or solvents.
To guarantee your gun remains in good working order, follow regular maintenance tips such as flushing the system with water or a cleaning solution after each use, and storing the gun in a dry, clean environment. By choosing a gun that's easy to clean and following these simple maintenance tips, you'll be able to work more efficiently and effectively, getting the job done right the first time.
Water-Based Sealer Pump Systems
During the concrete sealing process, a water-based sealer pump system becomes essential for efficiently and accurately applying the sealant. You'll want a system that guarantees consistent and even application, as this directly impacts the sealer's performance and the overall water-based durability of the concrete.
When selecting a water-based sealer pump system, consider the following key features:
-
Pump Pressure: Look for a system that can maintain a consistent pressure of at least 100 psi to guarantee proper sealer penetration and coverage.
-
Flow Rate: A higher flow rate allows for faster application and reduced labor time, but be sure it doesn't compromise the sealer's performance.
-
Hose and Wand: A durable, kink-resistant hose and a comfortable, ergonomic wand design make the application process smoother and more efficient.
- Sealer Compatibility: Verify that the pump system is compatible with your chosen water-based sealer to guarantee peak performance and durability.
Low-VOC Sealer Laminator Tools
When applying water-based sealers, it's equally important to guarantee a strong, even bond between the sealer and concrete, which is where Low-VOC sealer laminator tools come into play. These tools are designed to provide a uniform application and prevent unevenness, bubbles, or pooling.
By using a laminator tool, you can achieve a consistent, thin layer of sealer, which is essential for peak performance.
One of the significant low VOC benefits of these tools is reduced emissions, making them a safer choice for you and the environment. Additionally, laminator tools allow for more precise control over sealer application techniques, enabling you to achieve a more even finish. This is particularly important when working with water-based sealers, which can be prone to pooling or unevenness.
When selecting a Low-VOC sealer laminator tool, look for features such as adjustable flow rates, ergonomic design, and durable construction. These features will enable you to work efficiently and effectively, providing a professional-grade finish.
Frequently Asked Questions
Can I Use a Sealer on Newly Poured Concrete?
When considering applying a sealer to newly poured concrete, you need to wait until the concrete curing process is complete.
This typically takes 28 days, depending on environmental conditions.
Premature sealer application can hinder the curing process, leading to a weaker, more porous surface.
Wait until the concrete has fully cured, then assess its readiness for sealer application.
How Long Does It Take for Sealers to Fully Cure?
When you apply a sealer to your concrete, you're probably wondering how long it takes to fully cure.
The curing time depends on various sealing factors, including the type of sealer, environmental conditions, and concrete porosity.
Typically, sealers can take anywhere from a few hours to several days to fully cure.
You'll know it's fully cured when the sealer reaches its maximum hardness and chemical resistance.
Make sure to follow the manufacturer's instructions for ideal curing times.
Are Concrete Sealers Suitable for Indoor Use?
Are you willing to risk compromising your indoor air quality and moisture retention with the wrong sealer?
When it comes to indoor use, concrete sealers must meet specific standards. Look for sealers that are VOC-compliant, non-toxic, and breathable to guarantee they won't trap moisture or release harmful fumes.
These sealers will protect your indoor surfaces while maintaining a healthy environment.
Can I Apply a Sealer Over Existing Coatings?
When applying a sealer over existing coatings, you'll need to guarantee coating compatibility to avoid unwanted reactions.
First, inspect the current coating's condition and type to determine if it's compatible with the new sealer.
Then, perform necessary surface preparation, such as cleaning and roughening the surface, to create a strong bond between the old and new coatings.
Do Concrete Sealers Provide UV Protection?
Did you know that UV rays can cause concrete to degrade at a rate of 1/4 inch per year?
You're right to wonder if concrete sealers provide UV protection. The answer is yes, many sealers offer UV resistance, which helps extend their longevity.
In fact, a good sealer can resist UV degradation for up to 10 years, depending on the type and quality of the product.
Conclusion
You've navigated the labyrinthine world of concrete sealing tools, and emerged victorious, armed with the knowledge of the crè me de la crè me of applicators.
From silane-based sealer wands to polyurethane sealer brush masters, you've seen it all.
Your concrete will be sealed tighter than a drum, thanks to the expertise you've gained.
With these 7 champions, your sealing game will be unstoppable - a force to be reckoned with, a symphony of silicone and acrylic harmony.
Related Posts
-
What Tools to Rent for a Concrete Home Reno
When tackling a concrete home renovation, you'll need to rent a variety of specialized tools to get the job done. For...
-
Top 10 Concrete Repair Tools for Small Fixes
You'll need the right tools to tackle small concrete repairs efficiently and effectively. When it comes to small fixe...
-
Top Tools for Concrete Adhesion Success
When it comes to concrete adhesion success, you'll need to wield the right tools and techniques to guarantee a strong...